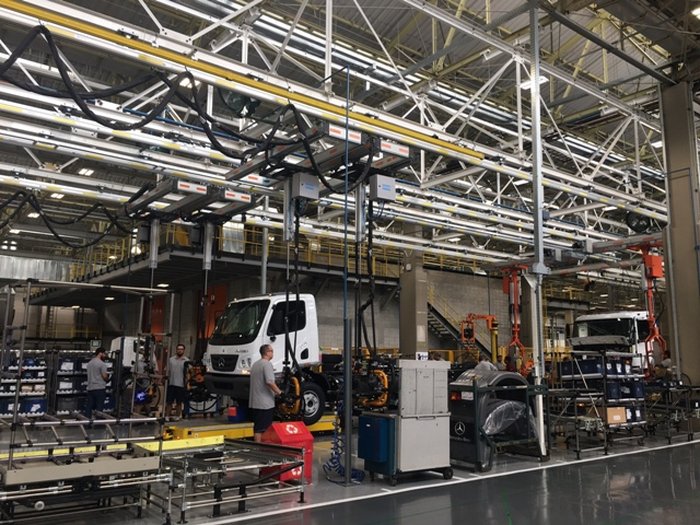
PRISCILA NUNES/Especial
São Bernardo do Campo
A modernização da fábrica de São Bernardo do Campo, em São Paulo, levou três anos, exigiu investimentos de R$ 500 milhões e deu um passo histórico rumo à implantação do conceito de Indústria 4.0 no país. Na semana passada conhecemos como ficou a antiga montadora de caminhões que se renova na sua trajetória de mais de 60 anos no Brasil. “Na Mercedes-Benz do Brasil já estamos vivendo o futuro”, comemorou o presidente da Mercedes-Benz do Brasil & CEO América Latina., Philipp Schiemer.
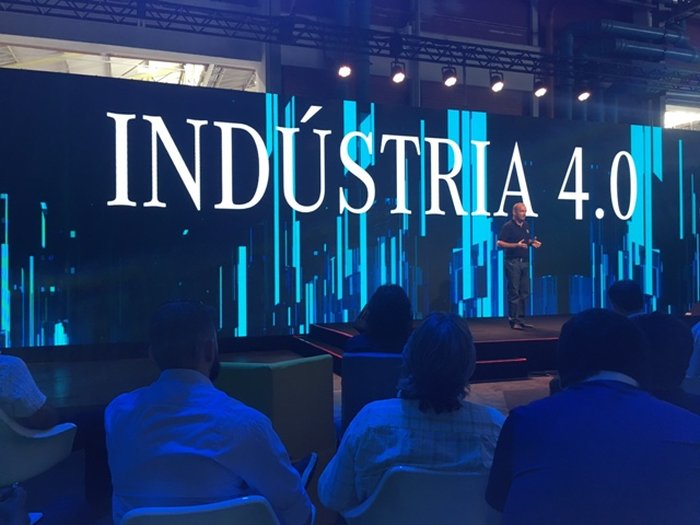
Foram três anos de construção, de 2015 a 2018, de um prédio renovado que concentra a montagem de caminhões, desde os leves aos pesados, e a logística de peças, num sistema moderno, integrado e inteligente de produção. Ao caminhar pela fábrica, logo no início já notamos a tecnologia digital e a conectividade na produção e logística. Trabalhadores e diversas funções organizadas em um espaço amplo. Chamou a atenção a circulação automática das peças de um setor para o outro, dispensando o trabalho manual.

O armazenamento de grandes volumes de dados na nuvem e o uso de tablets – elementos da Indústria 4.0 - foram aplicados à nova linha de montagem de caminhões da Mercedes-Benz. A essas características se juntarão ao uso cada vez mais intenso da Internet e das ferramentas virtuais de análise de dados em tempo real.
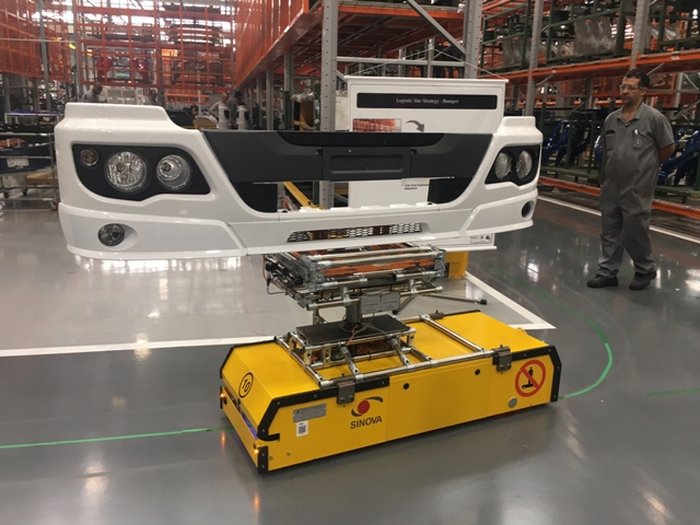
As peças circulam com o uso dos AGVs (veículos autônomos). São mais de 60 unidades que transportam os caminhões pela linha e pela área de logística, em conexão com as estações de trabalho onde são instalados todos os componentes. No fim da linha, após a conclusão da montagem, o AGV retorna ao ponto inicial com segurança orientado pelos diversos sensores e conexões ao longo do circuito instalado no chão de fábrica.

Outro ponto interessante é a substituição dos papéis por mais de 40 monitores de TV que orientam os montadores em cada estação de trabalho, com o conceito “Paper less”.
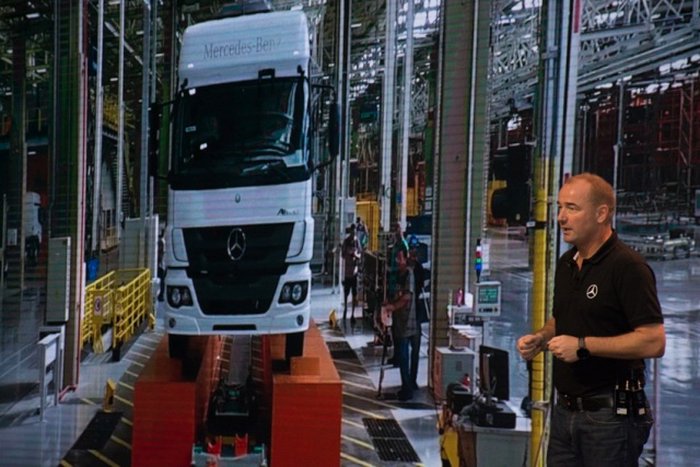
As tecnologias inovadoras da indústria 4.0 chegarão a todos os processos produtivos, como às linhas de agregados (motores, câmbios e eixos) e à fabricação de chassis de ônibus em São Bernardo do Campo, como também à planta de Juiz de Fora, em Minas Gerais, onde são produzidas as cabinas e os caminhões Actros.“Tudo isso está programado dentro do investimento de R$ 2,4 bilhões que anunciamos recentemente para os próximos cinco anos, até 2022”, comentou Schiemer.

A nova linha de montagem de trouxe ganhos para a empresa que ficou 15% mais eficiente em termos de produção do que a anterior. A eficiência logística alcançará 20% com a redução de armazéns de peças de 53 para seis e, o aumento de 20% para 45% da entrega de peças diretas na linha de e à redução do armazenamento de componentes de 10 dias para no máximo três dias.

Colaboradores foram ouvidos nas etapas do projeto da nova linha de montagem de caminhões e as sugestões são constantes. As apertadeiras eletrônicas da nova linha trabalham com o torque programado para cada produto. Eliminam erros e garantem a rastreabilidade do processo. São mais de 100 apertadeiras, em posições variáveis, a partir do teto, adequadas à estatura de cada montador para garantir ergonomia, segurança e produtividade.
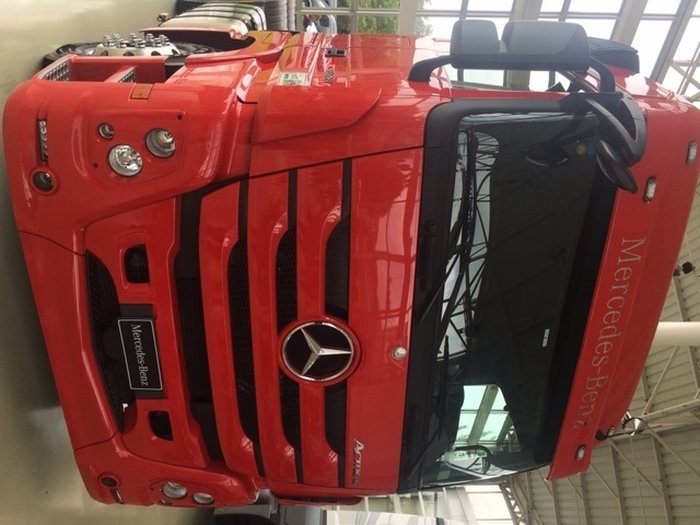
O uso de impressoras 3D assegura a rápida prototipagem de peças e agiliza o atendimento às demandas. A área de Protótipos pode testar novas peças com custo menor e mais agilidade. Em 2017, foram criadas mais de 150 peças em 3D internamente. O layout inovador é outra novidade da linha de montagem de caminhões. Com o conceito “One roof assembly”, todos os modelos de caminhões podem ser produzidos no mesmo prédio, com a flexibilidade de ordem de montagem de qualquer modelo, do leve ao pesado.
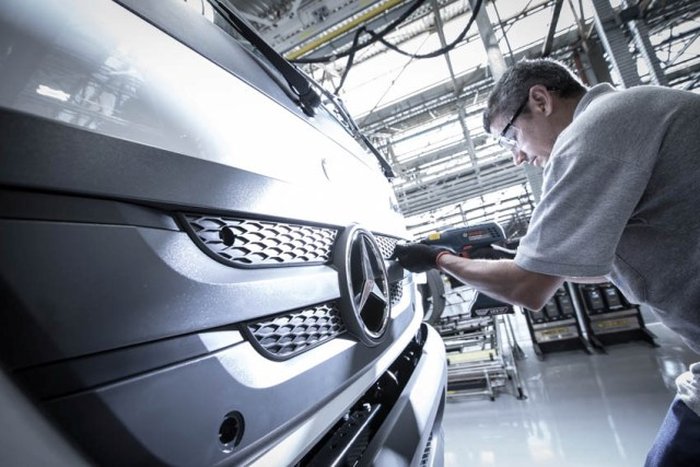
O conceito “Fishbone” resulta em estoque e supermercado de peças, pré-montagem e montagem final totalmente integrados, otimizando e agilizando o processo de produção de caminhões. A unificação e verticalização dos almoxarifados possibilitou a centralização do recebimento, distribuição e devolução de embalagens vazias. O que resultou em ganhos de produtividade e eficiência, redução de custos de logística e transporte dentro da fábrica.
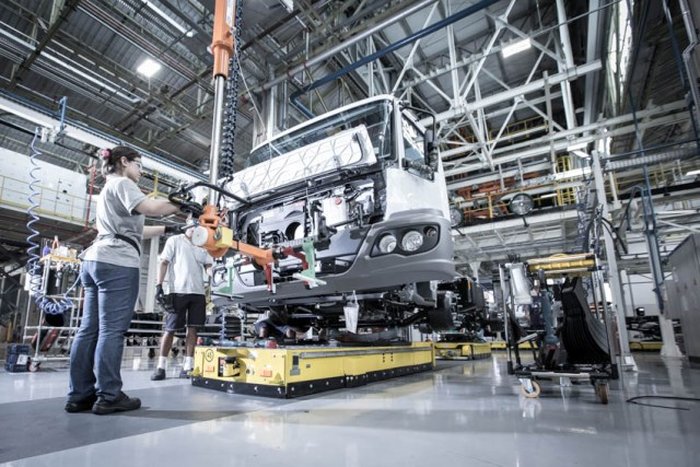
As novas empilhadeiras contam com câmeras orientam toda a movimentação, o que garante eficiência e segurança ao processo de logística de abastecimento de peças, componentes e conjuntos na linha de produção. Sensores luminosos nas prateleiras de estoque monitoram a entrada e a saída de materiais e alimentam de informações toda a cadeia de suprimentos da linha.

Os mais de 50 antigos armazéns logísticos serão concentrados em seis Hubs Logísticos – 12 metros de altura - integrados à linha de montagem. Próximos a um centro de produção, melhoram a ergonomia e a segurança dos colaboradores, garante mais rapidez na produção e maior agilidade de processos, além da diminuição nos custos de transporte.

A nova fábrica traz ganhos para o ambiente e contribui para uma operação mais sustentável. Com a adoção de lâmpadas LED em 100% da linha de montagem final de caminhões o consumo de energia foi reduzido em 56%.
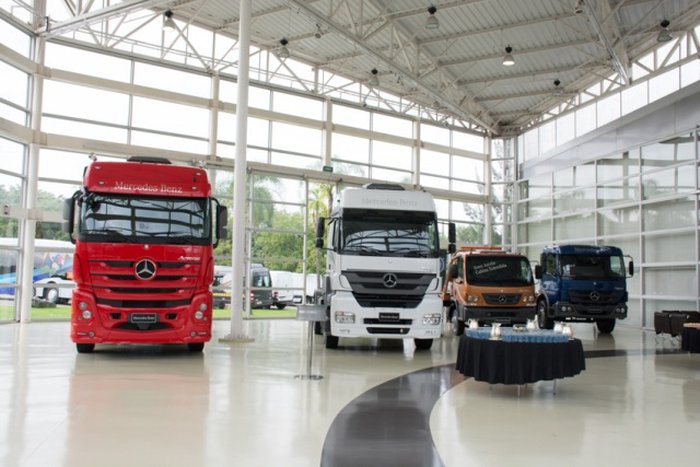
Viagem a convite da Mercedes-Benz