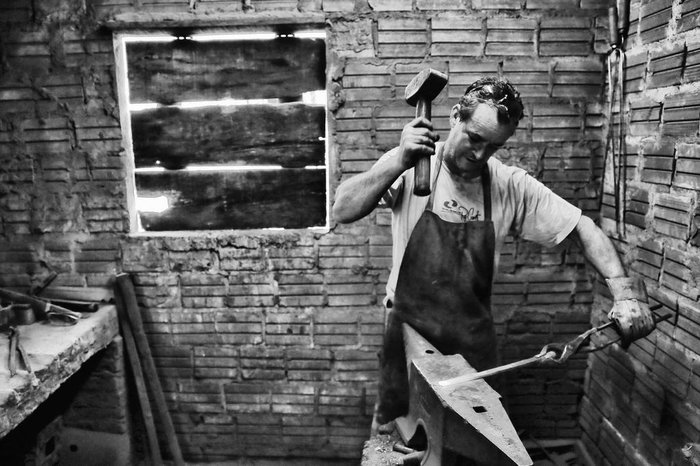
A cutelaria artesanal é quase uma poesia concreta. Não que da forja saiam palavras em algum formato sugestivo. Nada disso. Mas o processo que resulta na transformação de qualquer peça de aço em uma faca artesanal é de uma beleza ímpar. Engolido pelas labaredas, o objeto metálico original deixa a fornalha ainda em brasa. Com o alicate em uma das mãos, o cuteleiro gira a peça incandescente de um lado para o outro, enquanto a martela contra a bigorna - de forma alternada, em um lado de cada vez.
A mágica metamorfose dos mais variados itens em facas artesanais é emoldurada pelo som metálico do aço espremido entre a marreta e a bigorna. E, seja lá o que entra na forja (molas de trem, discos de arado agrícola, serras, chassis de motosserra, rolamentos, brocas de furadeiras), o que sai, invariavelmente, é a base de uma belíssima lâmina artesanal. Arte pura.
Foi justamente este poema visual que seduziu Leonel Felden, 45 anos. Uma década e meia atrás, quando visitou a cutelaria de Eliseu Souza, Leonel se apaixonou pelo que viu - o fogo, o aço bruto transfigurado em brasa, as fagulhas no ar, o nascimento de uma faca. Decidiu que dali em diante faria aquilo da vida: seria cuteleiro. E se tornou sócio de Eliseu:
- Vi o Seu Eliseu forjando. Me deu aquela curiosidade. E tive em mente que sabia fazer aquilo ali. Tinha condições de fazer como ele fazia - conta Leonel, hoje sócio do filho de Eliseu, Patrick Souza, na cutelaria Felden e Souza, em Santa Maria, na Região Central, centro cuteleiro com quase 30 fábricas, entre elas mais de 20 de facas artesanais.
Conheça o trabalho do domador, um guardião das tradições do RS
Sal que preserva a memória: o trabalho do produtor de charque no RS
De imediato, é preciso explicar que existem, basicamente, dois tipos de facas artesanais: as comuns, como as feitas de discos de arado e outros objetos de formato laminado, e as forjadas, produzidas a partir de peças de formato não laminado, que exatamente por isso dão mais trabalho e, ao mesmo tempo, passam por um processo mais complexo - e bonito - de fabricação.
- A parte mais prazerosa é quando vejo a faca forjada. Ela não precisa nem estar pronta. Quando vejo a peça forjada, eu digo: esta deu certo - explica Leonel.
Por utilizarem objetos mais difíceis de serem moldados, como molas de trem, por exemplo, as facas forjadas levam de dois a três dias para ficarem prontas. Isto porque o objeto inicial, depois de muitas marteladas e em diferentes estágios, precisa mudar completamente de formato até ficar chato e delgado como uma faca - "espichado", como dizem os cuteleiros. Com isso, é claro, a faca custa mais caro do que a comum, algo entre R$ 600 e R$ 800.
Patrick (esq.) e Leonel são responsáveis por todo o processo de confecção
das facas na Felden e Souza, em Santa Maria, no centro do Estado
Os modelos artesanais comuns exigem menos esforço. Um disco de arado já tem formato achatado, e, uma vez cortada, a peça só precisa ser endireitada, perdendo o formato abaulado original. Depois de uma hora e meia a duas de trabalho, o produto final está pronto, com preço a partir de R$ 120.
Clássicos Gauchescos: Pedro Ortaça conta a história da música "Timbre de Galo"
Da mesma forma que as lâminas, os cabos também podem ser feitos de vários materiais. Os principais são madeira, chifre de boi, prata e ouro. Na Felden e Souza, o chifre de boi é endireitado em uma prensa e, depois, afixado na faca por meio de pinos metálicos. Já os acabamentos em ouro e prata são produzidos por uma empresa terceirizada, com sede em Santo Ângelo, nas Missões, e depois encaixados no produto final pelos próprios cuteleiros, em Santa Maria.
Mais mecanizada e com mais funcionários do que a Felden e Souza, a Facas Quadros, de Viamão, na região metropolitana de Porto Alegre, também produz facas artesanais a partir de discos de arado e de inúmeros outros itens de aço. O atual proprietário, Leandro Quadros, 39 anos, começou na cutelaria há três décadas, ainda criança, ajudando o pai, Walmor Quadros, que criou a empresa em 1971.
A verdade sobre o trecho do hino gaúcho que os deputados cortaram há 50 anos
Atualmente, fabrica de 200 a 300 facas por mês. As produzidas com discos de arado são as que têm mais saída. Para produzi-las, primeiro, usando um giz comum, desenha-se o formato do item sobre o disco de aço. Depois, com uma espécie de maçarico, corta-se a peça de acordo com o desenho. A faca tem o seu primeiro esboço em metal.
No esmeril, uma tempestade de faíscas engole o cuteleiro
A próxima etapa é a passagem da peça no esmeril, com o objetivo de aparar imperfeições, momento em que o cuteleiro se vê engolido por uma tempestade de faíscas. Depois, a faca é colocada na forja, uma fornalha de alta temperatura, que pode chegar a 900°C ou 1.000°C. Dali, ela sairá como uma brasa, mais mole do que em estado natural, facilitando ao forjador o trabalho de compactação da lâmina onde ficará o fio.
A seguir, o artefato passa novamente pelo esmeril e ganha a estampa da cutelaria, aplicada com uma espécie de carimbo de metal. Por fim, as etapas de têmpera (mergulho do aço com o objetivo de aumentar a sua consistência e rijeza) e revenimento (ato de dar a temperatura ideal a uma peça de aço), e a faca está quase pronta para ser embainhada por algum gaudério. Falta apenas o cabo, também produzido à parte.
- Gaúcho que se preze não vive sem uma faca - resume Leandro.
Na Idade Média, cidades como Toledo (Espanha), Sheffield (Inglaterra), Solingen (Alemanha) e Thiers (França) eram polos da cutelaria. No Brasil, embora o primeiro registro da atividade remeta ao ferreiro português Bartolomeu Carrasco, que teria instalado uma oficina às margens do Rio Jurubatuba, no litoral paulista, a fabricação de facas só viria a despontar a partir de 1718, na localidade de Pasmado (PE).
Cada artefato é diferente
Com pequenas adaptações, a tecnologia empregada na cutelaria artesanal contemporânea é a mesma de séculos atrás. Antigamente, as forjas eram "tocadas" (ventiladas) a fole e a pedal. Hoje, um pequeno motor elétrico empurra o ar fresco para o interior da fornalha, fazendo com que as brasas fiquem mais vivas, e o fogo, mais intenso. Entre os materiais usados na confecção do cabo, o mais comum é o chifre de boi, usado pelos antigos ferreiros, que fabricavam os instrumentos de corte nos idos dos farrapos.
- Fazemos tudo manualmente, a fogo, martelo e bigorna. Tivemos de aperfeiçoar algumas coisas, mas a técnica de fazer a faca é a que se usava na época da Revolução Farroupilha - explica Patrick Souza, 38 anos, sócio da Felden e Souza.
Da mesma forma que as lâminas, cabos também são feitos de vários materiais
Segundo ele, muitos clientes levam diversos objetos de aço para serem forjados e transformados em facas. Uma das peças mais curiosas que chegaram à cutelaria é um pino da lagarta (esteira) de um carro de combate norte-americano M-113, modelo em operação desde 1960 e utilizado em conflitos como Guerra do Vietnã, Guerra Irã-Iraque, Operação Tempestade no Deserto e Guerra do Kosovo.
Clássicos Gauchescos: Mauro Moraes conta a história da música "Milonga Abaixo de Mau Tempo"
Além dos materiais trazidos pelos clientes, Leonel e Patrick utilizam materiais descartados como sucata - uma mola de trem, que custa R$ 20 no ferro-velho, por exemplo, é base para a fabricação de 20 facas. Com matérias-primas diversas e sem maquinário para a fabricação em série, o resultado é que cada faca é um produto único, diferente daqueles já criados pela dupla.
- Nunca fazemos uma faca igual a outra. Para que fossem iguais, teríamos de ter tecnologia. E não temos. É uma a uma - garante Patrick.