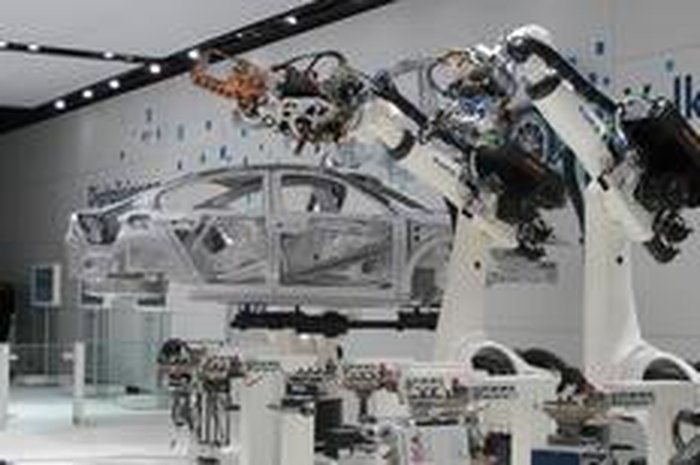
Sem barulho e nem faíscas, braços mecânicos levantam peças de forma sincronizada e encaixam cada uma no seu exato lugar. Boa parte dos funcionários acompanha tudo à distância, por telas de computadores. A harmoniosa interação dos seres humanos com robôs, a chamada indústria 4.0, começa a dar forma a uma nova era na economia mundial.
Na cidade alemã de Wolfsburg (a 180 quilômetros a oeste de Berlim), que abriga a maior fábrica de automóveis da Europa, é possível constatar como será o futuro das linhas de produção inteligentes. A sede mundial da Volkswagen tem mais de 50 mil funcionários em um complexo gigantesco, onde são produzidos dois carros por minuto.
Poucos humanos são vistos nas linhas de montagem. A maioria supervisiona o trabalho das máquinas de longe, por meio de softwares. São quase 6 mil robôs trabalhando 24 horas por dia para fabricar os modelos Golf A7, Tiguan, Touran e Golf Sportsvan. Onde força e mente humanas são necessárias, homens ficam lado a lado dos robôs. Em vez de trabalhar isolados, com a premissa de perigo, as máquinas interagem com os funcionários, como se fossem colegas.
Com robôs se comunicando entre si, trocando informações, status e problemas, as fábricas inteligentes não dependem apenas de pessoas para a tomada de decisões. Conectadas em rede, em um ambiente em que todos os equipamentos estão interligados, as máquinas podem determinar o que as outras devem fazer.
A nova era industrial, também batizada de internet das coisas, tem como característica ainda a quantidade de informações digitais, de estoques de materiais a organização da linha de produção, além do gerenciamento de energia. Com um consumo de luz equivalente a quase 500 mil residências, o complexo industrial da Volkswagen em Wolfsburg tem um programa específico para controle de energia, água e resíduos.
- Grande parte da energia ainda vem do carvão. Estamos trabalhando para substituí-la por óleo e gás e por fontes renováveis, como eólica e solar - explica Karsten Bosse, responsável pelo gerenciamento de energia da montadora.
Não por acaso, a indústria alemã investiu mais de 40 bilhões de euros (cerca de R$ 131,2 bilhões) nas fábricas inteligentes nos últimos quatro anos. E os investimentos vão além do ramo automobilístico.
- Essa transformação provocará mudanças profundas na manufatura mundial - destaca o presidente da Federação das Indústrias do Rio Grande do Sul (Fiergs), Heitor Müller, que liderou missão empresarial no mês passado à Feira Industrial de Hannover, maior evento de tecnologia industrial do mundo.
Brasil ainda está distante da nova era
A indústria 4.0 é motivada por mudanças no setor produtivo que vão da imensa quantidade de informações digitalizadas a novas estratégias de inovação em pessoas, pesquisa e tecnologia.
- Entramos na era da indústria integrada, onde a tecnologia da informação pensará todo o processo de produção - explica Ronald Josef Zvonimir Dangel, diretor do Instituto Senai de Inovação e Soluções Integradas em Metalmecânica.
Dangel explica que um dos recursos usados pelas fábricas do futuro é o comissionamento virtual, que possibilita a programação das máquinas por meio de softwares. Enquanto a nova fase industrial é realidade em modernos complexos da Europa e dos Estados Unidos, no Brasil a mudança ainda é um conceito pouco difundido.
- Temos algumas experiências isoladas no Brasil em direção a esse futuro, bem distante da realidade da Alemanha - afirma Dangel, que participou da missão de empresários à Feira Industrial de Hannover, na Alemanha.
Pesquisa realizada em 1,5 mil empresas de diferentes setores do Rio Grande do Sul revela que a maioria das indústrias gaúchas está ainda entre a segunda e a terceira revolução industrial.
- As indústrias locais inovam muito pouco. Estão focadas na redução de custos, o que acaba impactando na qualidade dos produtos - avalia Paulo Zawislak, coordenador da pesquisa e professor da Escola de Administração da Universidade Federal do Rio Grande do Sul (UFRGS), que fez o estudo em conjunto com mais três universidades gaúchas.
Atraso maior no maquinário
Para Zawislak, o atraso brasileiro está mais relacionado aos processos e às máquinas pouco avançadas tecnologicamente do que à mão de obra disponível.
- A cultura brasileira é retardatária. Achamos que o sucesso de um empreendimento tem a ver com número de postos de trabalho gerados, enquanto a Europa e os EUA estão focados em competências técnicas que só eles têm. A lição de casa é bem mais profunda - acrescenta.
Avanços do século 18 ao 21
1ª Revolução
O aperfeiçoamento da máquina a vapor por James Watt, no século 18, colocou a indústria têxtil como símbolo da produção excedente, gerando a riqueza da época e criando um novo modelo econômico. Entre 1760 e 1860, a primeira revolução ficou limitada, primeiramente, à Inglaterra. Houve o aparecimento de indústrias de tecidos de algodão, com o uso do tear mecânico.
2ª Revolução
A segunda etapa ocorreu no período de 1860 a 1900, quando Alemanha, França, Rússia e Itália também se industrializaram. O emprego do aço, a utilização da energia elétrica e dos combustíveis derivados do petróleo, a invenção do motor a explosão e da locomotiva a vapor e o desenvolvimento de produtos químicos foram as principais inovações desse período.
3ª Revolução
Considerada a era da automação, a terceira fase ganhou forma com o uso de computadores no chão de fábrica, colocando controles eletrônicos, sensores e dispositivos capazes de gerenciar uma grande quantidade de variáveis de produção, permitindo a tomada de decisões de controle de dispositivos de forma autônoma. A fase durou cerca de 40 anos, de 1969 a 2010.
4ª Revolução
Ocorre a interação máquina com máquina. Os sistemas passam a trocar informações entre si, de forma autônoma, tomando decisões de produção, custo e contingência. Fábricas inteligentes usam equipamentos e mão de obra altamente tecnológicos.
* A repórter viajou para a Alemanha a convite do Sebrae/RS